Report: Inline in Plastics in Magazine
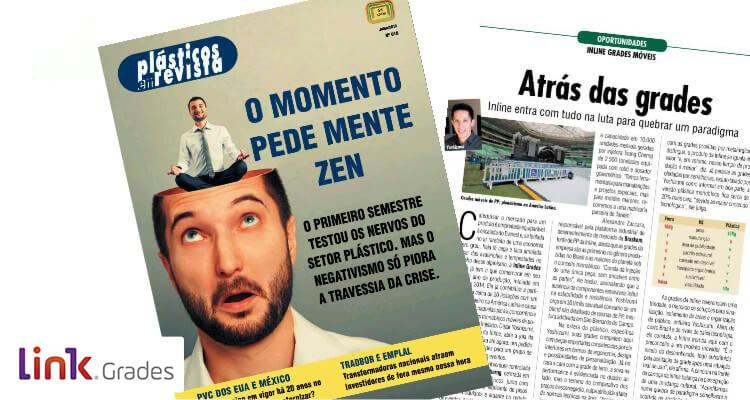
- 26 de abril de 2015
Check out the Report on the innovative Inline barricades in Plastics in Magazines, our director speaks of the challenges of manufacturing the World's Largest Plastic barricade!
Inline enters with everything in the fight to break a paradigm
"Catching the market for a product is a contract that is comparable to the escalation of Everest, and if attempted in the rarefied air of a zero-degree economy, there is blind faith and a blunt knife. In spite of the avalanches and storms in the way of this mountain climbing, Inline Grades Móveis already has what to commemorate in its first year of production, begun in August 2014. It already counts the participation in about 20 biddings with a pioneering product in Latin America and cause of migraine of those for the metallic competition: monobloc barricade movable of polypropylene (PP) injected. César Yoshizumi, CEO of Inline, opens the crown jewel of his portfolio so far: an initial order of 1,500 grids for a group of event companies.
Inline is a joint venture controlled by Taiwan's Tsong Cherng, focused on injection molds and peripherals, along with Brazil's CriaDeck, a manufacturer of modular plastic floors and active in the event center. At the plant in São Bernardo do Campo, São Paulo, Yoshizumi places the capacity at 10,000 monthly units generated by a 2,500 ton Tsong Cherng injector equipped with a robot and gravimetric meter. "We have tooling for maintenance and special projects, but for larger molds, we use a partner matrix from Taiwan."
Alexandre Zaccara, in charge of Braskem's industrial platform for market development, source of Inline's PP, attests that the company's barricades are the first in the genre produced in Brazil and the largest in the world under the monoblock concept. "It consists of the injection of a single piece, without fittings between the parts," he translates, noting that the absence of removable components influences stability and resistance. Yoshizumi estimates its current consumption of a non-detailed blend of PP resins at 30 t / month, a mixed blend in São Bernardo do Campo.
In the sphere of plastic, Yoshizumi specifies, his grids compete here with imported pieces considered by him inferior in terms of ergonomics, design and possibilities of personalization. Already in the face to face with the iron grid, the blow in the performance is evidenced in the table next, but the terrain of the price comparison is slippery, fault attributed to the lack of technical standards in the area. "So each mobile rail supplier has developed products with particular specifications," argues the director. But if faced with the grids supplied by metallurgists, it distinguishes, the product of Inline equals in value "and in volume, our production time is smaller," he says. Already facing the grids offered by locksmiths, a redoubt rated by Yoshizumi as informal in large part, the monoblock plastic version is about 20% more expensive, "due to the greater technological content," he judges.
Inline railings revere a trinity: the market for solutions for signaling, isolation of areas and organization of the public, lines Yoshizumi. In addition to the cost of Brazil and low-tech rivals, he says, Inline stumbles here with the prejudice of an innovative product. "It is the fear of the unknown, soon replaced by the acceptance of the barricade after a real situation of use," he says. The carrot in front of the Inline wagon rocks in the pursuit of cultural change. "We believe in a paradigm break similar to the one that occurred in the abolition of old folding iron chairs by the plastic monoblock, effect of their lightness, beauty and ease of transportation and storage," Yoshizumi said.
Source: http://plasticosemrevista.com.br/atras-das-grades/
PDF Review: http://plasticosemrevista.com.br/pdf/plasticos_616.pdf